Our strategy is linked to our Vision, Mission and Values. The planning process takes into account both external and internal business environment and factors in risks, opportunities, challenges and past learnings. Our overall strategy and plans are cascaded down to individual divisions/departments with clearly defined responsibilities across all employee levels.
INTEGRATED STRATEGY PLANNING PROCESS
for Strategy Formulation and Resource Allocation
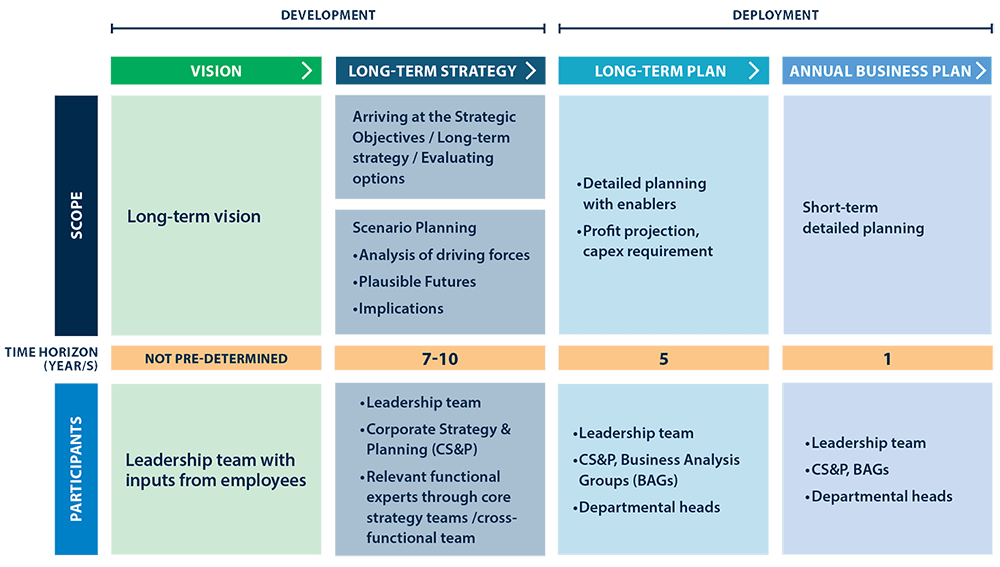
Our long-term strategies and annual business plans are formulated as an outcome of this process. Our capital provisions are thus formulated, having been aligned with strategies at the beginning of the year. These include:
Annual and five-year capital expenditure plans
Corpus for small capital expenditure schemes related to safety, environment and other improvement projects
CSR and R&D budgets
Projects & partnerships with stakeholders (customers, suppliers, industry bodies and communities) and technological collaboration with academia and technology partners are identified and/or reviewed for implementing the identified strategies. Functional teams take suitable actions to ensure the availability of resources through their respective plans. These are cascaded to individual key result areas comprising following elements:
Individual contribution for meeting strategic objectives in the respective functions
Identifying the training needs for the year
Cross-functional projects
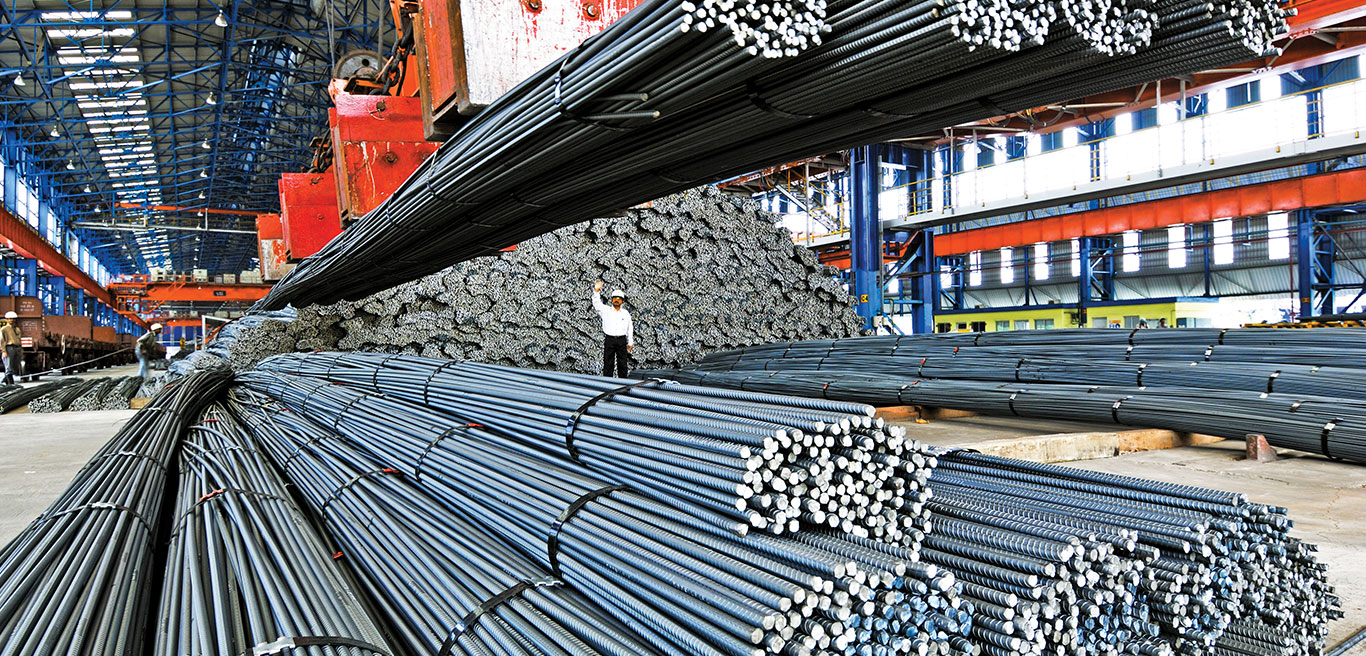
Tata Steel Jamshedpur
Our business environment is influenced by global macro-economic conditions, developments in steel and allied industries and the ever-evolving technological landscape. Apart from this, the social context in the areas we operate in (legislative, regulatory and political) affect our overall ecosystem.
Tata Steel India is well placed to capitalise on India’s growth. Though FY2017 was a challenging year, India is poised for a 5-6% increase in the steel demand compared to the previous year.
MACRO-ECONOMIC
3.1%
Global GDP Growth
Overall global recovery in manufacturing and global trade
7.1%
Indian GDP Growth
In India services continued to support growth
STEEL DEMAND
1,515 MnT
Steel Demand Globally
Global Steel demand grew by 1% mainly due to recovery in China
78 MnT
Indian Steel Demand
Indian steel demand saw a modest growth of 3% due to low growth in construction sector and impact of demonetisation coupled with decline in imports
RAW MATERIAL
CFR - 64 $/t
Iron ore contract price
Came down compared to FY2016 due to continued oversupply, high demand in China and delay in operationalisation of new mines
FoB -165 $/t
Coking coal - QBM Price
Went up compared to FY2016 due to disruption in mining operation in Australia and reduction in number of working days in China
Risks
We are exposed to risks arising out of the dynamic macroeconomic environment as well as from internal business environment. These could adversely affect our ability to create value for our stakeholders.
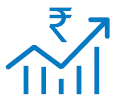
MACROECONOMIC
Over capacity and over supply in steel industry
High levels of imports
Consolidation among competitors
Local circumstances of geographies we operate in
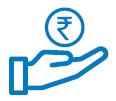
FINANCIAL
Volatility in financial markets and fluctuations in exchange rates
Downgrading of credit rating of Company’s securities
Substantial amount of debt
Restrictive covenants in financing agreements
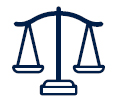
REGULATORY
Predatory pricing
Non-renewal of mining leases
Non-availability of protective trade measures
Regulatory and judicial actions
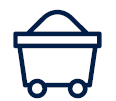
OPERATIONAL
Highly cyclical industry
Inability to implement growth strategies
Inherently hazardous industry
Volatility in raw material prices
Hostilities, terrorist attack or social unrest
Failure of Information Technology Systems
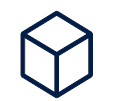
MARKET RELATED
Competition from alternate materials
Product liability claims

CLIMATE CHANGE
International and domestic regulations relating to Green House Gas emissions
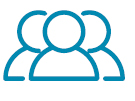
PEOPLE
Continued services of Senior Management
Unanticipated labour unrest
Opportunities
Setting benchmarks in the sector, we monitor and leverage opportunities presented by the external and internal environment.
Capitalising the demand growth, due to urbanisation and needs of a young demography in India, and developmental needs of other emerging economies
Leveraging Supportive schemes of the Government such as the “Make in India” initiative
Securing raw-material supplies by investing in mines which are in close proximity
Innovating and adopting new technologies through Company-wide mobilisation of resources, implementation of pilots and capacity development
Value realisation of by-products by exploring new areas of application, collaboration and potential customers
Creating differentiation through acceleration of new product development, growing revenue from services & solutions and the B2C segment
Committed to Zero
'Committed to Zero' is our top priority, with the target of having Zero Lost Time Injuries (LTIs). Our senior leadership believes in promoting a safe working environment across the organisation and has taken the onus of being a role model to showcase paramount importance of workplace safety, which is embedded as a core value in our culture. We were conferred the Safety and Health Excellence recognition 2016 in 'Leadership' category by the World Steel Association.
During the year, we saw an increase of 19% in LTIs over FY2016 and 5 fatalities in different divisions. These incidents have been investigated and corrective actions are in progress. Safety of our work force is our utmost priority and we draw lessons from these unfortunate incidents. We continuously strive towards achieving our goals of zero fatalities at work place and eliminating injuries and occupational diseases across the organisation.
During the year, we further mechanised some of our operations, implemented rigorous safety line walks, recalibrated on managing redundant assets, strengthened the deployment of contractor safety management and embraced digital intervention to reduce human interface.
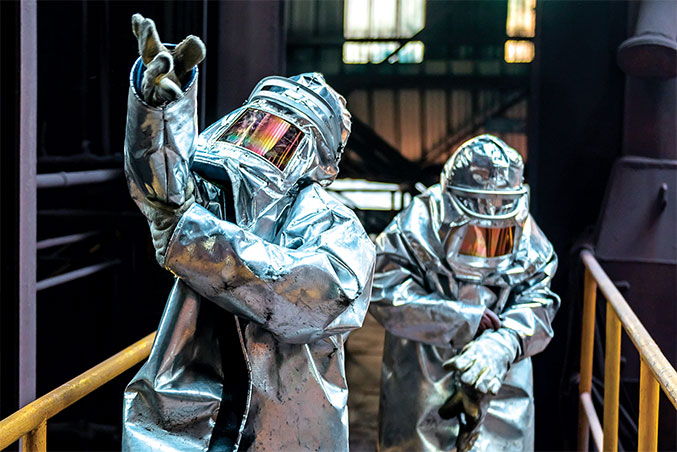
STRATEGIC FOCUS AREA
Safety - Committed to Zero
STAKEHOLDERS
People working at our sites
OUR GOAL
'Committed to Zero'
Zero LTI
ENABLERS
Build Leadership Capability
Competency development for hazard identification and risk management
Management of contractor safety
Focus on process safety
Improvement in occupational health and industrial hygiene
CAPITALS IMPACTED
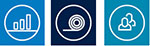
UN SDG
3 - GOOD HEALTH & WELL-BEING
Safety and Health Excellence
Recognition 2016 in 'Leadership'
Category By World Steel Association
INITIATIVES AND IMPACT
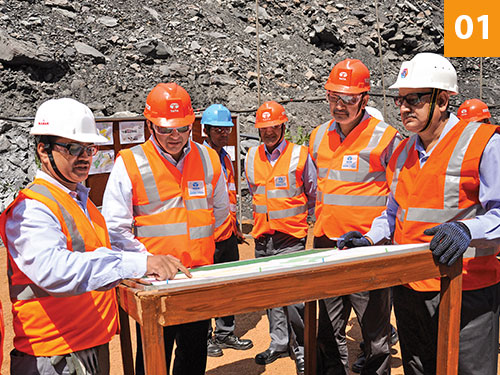
FELT LEADERSHIP
Felt leadership training imparted to a large section of officers, front line supervisors and union members at all locations of Tata Steel India
Leadership team have challenged themselves by targeting Zero in all key safety performance parameters.
2,959 Officers
2,173 Non-Officers
Trained

COMPETENCY & CAPABILITY DEVELOPMENT
Supervisors’ training on hazard identification and risk management
Quarterly safety campaigns conducted for the below mentioned categories which were the major contributors for Loss Time Injury (LTI)
Categories - Slip/ Trip/ Fall & Hit/ Press by object, Material Handling, Rail & Road Safety and Moving Machinery
2,173 Frontline Employees
Trained
The campaigns helped identify and mitigate hazards in the identified categories
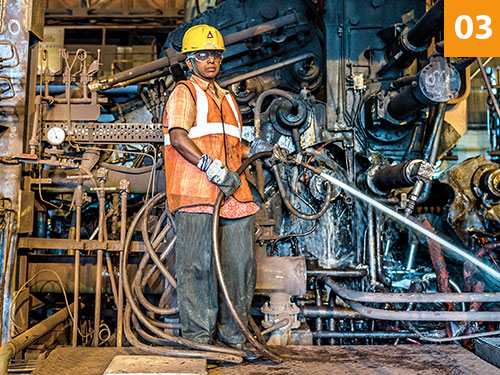
CONTRACTOR SAFETY RISK MANAGEMENT
Deployed safety capability assessment system
Launched vendor assessment based on a star rating system for high risk jobs
Conducted independent Audit for Contractor Safety Management
852 Vendors
Assessed
More than 50% vendors achieved star rating of 3 thereby demonstrating safe work practices
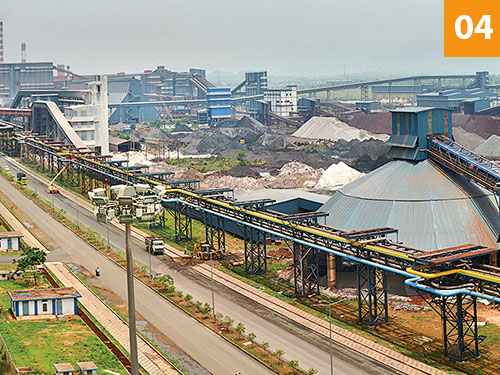
ROAD & RAIL SAFETY
Focus on rail & road safety initiatives such as ‘Safe Drive” Training Programme, Mass transport facility engaging contract partners, etc. were launched
Zero fatality on road for last 2 years
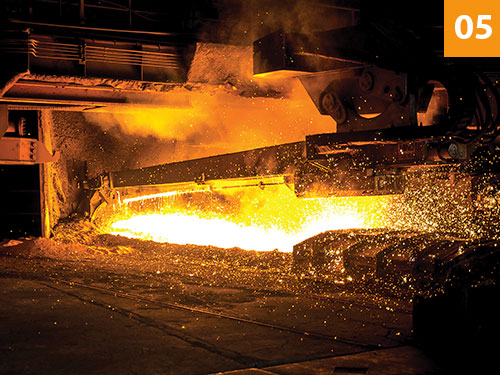
PROCESS SAFETY MANAGEMENT
Standard for Management of Change
Centre of Excellence (COE) setup for increased sensitisation on process safety and horizontal deployment initiated
No fatality in Jamshedpur Works in FY2017
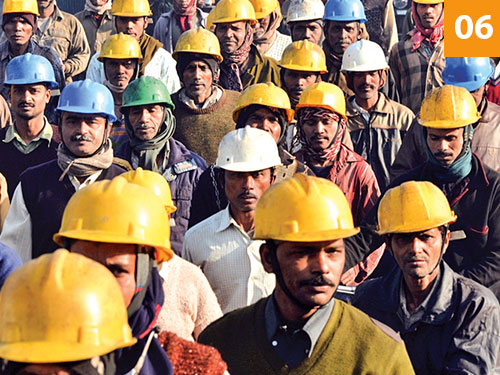
OCCUPATIONAL HEALTH / INDUSTRIAL HYGIENE (OH/IH)
Implemented 4 pilots on Qualitative Industrial Hygiene to facilitate identification of occupational health hazards and risk analysis
Launched focused awareness and intervention programmes like Doctor@Doorstep, Doctor Online and observance of health days
Improvement in Health |
52% reduction in |
KEY PERFORMANCE INDICATORS
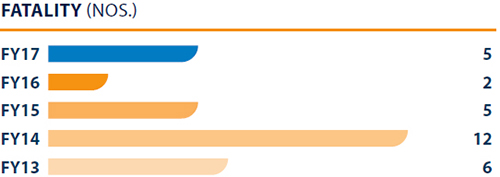
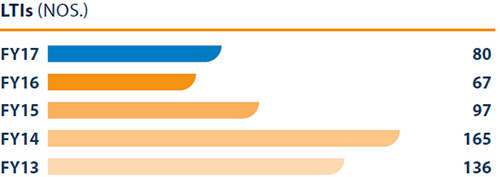
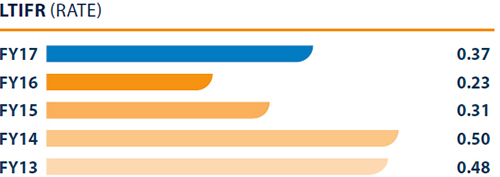
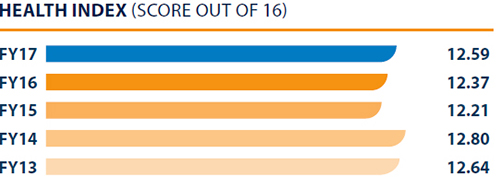
Our people practices are aimed at developing a culture of care, commitment, engagement and harmony across the workforce. There is increased focus on encouraging diversity, through inclusion of women, underprivileged sections of the community and people who are specially abled. At the same time, we strive to increase productivity while containing wage cost. This continues to be a challenge, making it imperative for us to rationalise, upskill and redeploy workforce without disturbing the industrial harmony that has been the bedrock of our organisation.
GARNERING TALENT
We conducted a variety of on-campus programmes like 'Mind Over Matter’ for technology schools and 'Steel-a-thon’ for business schools. We aim to achieve an 80% conversion rate on our pre-placement offers to suitable candidates.
DIVERSITY & INCLUSION
In order to improve employee work-life balance, among others, we rolled out the following policies like paternity leave, increased maternity leave, work from home, etc.
Satellite Work Operation
Aimed at providing flexibility, this policy enables employees to work from any location
where the Company has presence other than the employees’ base location for a specified
period of 1 or 2 years.
Women of Mettle
One of the first programmes in the manufacturing industry in India, Women of Mettle
goes beyond providing scholarships. The programme gives women from select
engineering colleges the opportunity to work with Tata Steel and experience
real-life technical challenges in the steel industry. The programme also gives students the
opportunity to interact with senior leadership who act as tutors and mentors.
STRATEGIC FOCUS AREA
Employer of Choice
STAKEHOLDERS
Current and Prospective Employees
OUR GOAL
To be in the top quartile ranking in India across industries
ENABLERS
Attract and nurture a diverse workforce
20% women in workforce
Improve workforce engagement and happiness
CAPITALS IMPACTED

UN SDG
8 – DECENT WORK & ECONOMIC
GROWTH
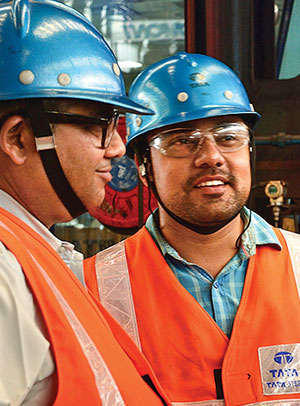
ENABLERS AND IMPACTS
KEY ENABLERS | |||
Culture of union and management working together through joint consultative process to address issues related to collective bargaining |
Focus on Diversity and Inclusion |
Employee capability building through structured training & development programmes |
Innovative and attractive voluntary separation scheme |
IMPACT | |||
89 years of industrial harmony |
15% increase in
the women in the
workforce over
FY2016 |
3,34,050 man-days of training imparted during FY2017 |
Increase in Employee Productivity by ~3% over FY2016 |
KEY PERFORMANCE INDICATORS
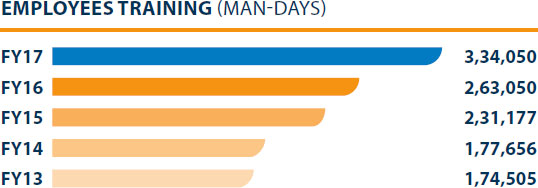
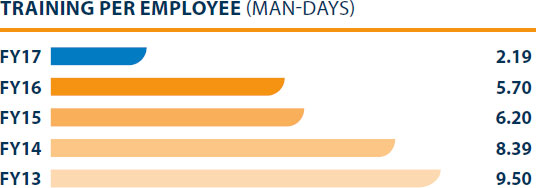
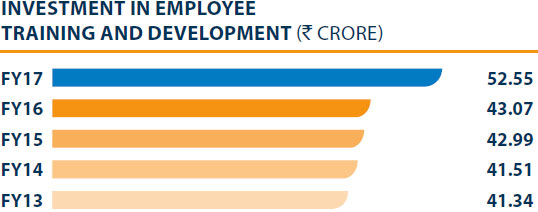
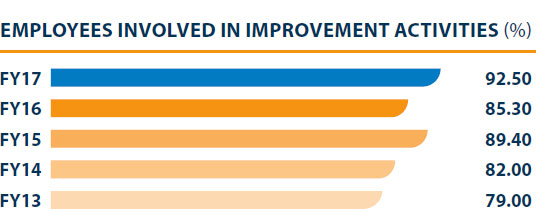
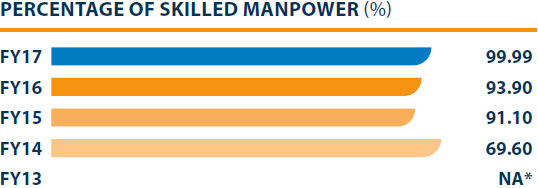
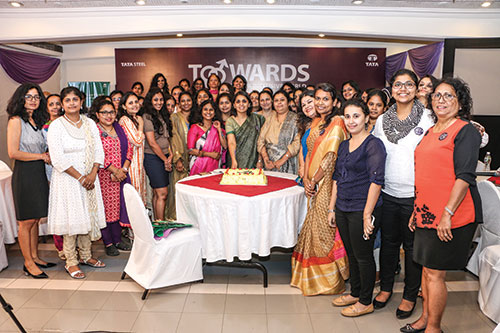
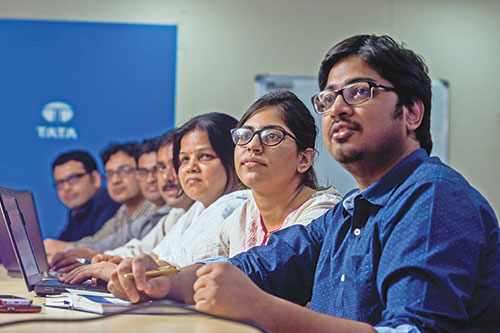
It is imperative for us to keep pace with the growing needs of our customers across sectors, primarily, the automotive and construction sectors. We aim to deliver enhanced value for our customers through our customised services and solutions and our value-added products. To insulate our business interests from cyclicity of the industry, we are foraying into new lines of business.
Tata Steel’s Greenfield plant at Kalinganagar in Odisha (the largest in the country) commenced commercial production from May 2016 with a capacity of 3 MnTPA in its first phase. The plant produces world-class flat, lighter, high-tensile strength steel and has augmented our Indian crude steel production to around 13 MnTPA. It has helped the organisation expand its portfolio to high-grade flat products to cater to a range of sectors including ship-building, defence equipment, energy and power, infrastructure building, aviation and lifting and excavation. Seven new product licences and nine higher grades in existing product licence have also been granted by the Bureau of Indian Standard for products manufactured at our Kalinganagar plant.
Tata Steel Kalinganagar has achieved the fastest rampup in a Greenfield project in India. Crude steel production in FY2017 was 1.68 MnTPA. The crude steel capacity was ramped up to 88% with the Coke plant & Hot Strip Mill reaching 100% capacity in FY2017.
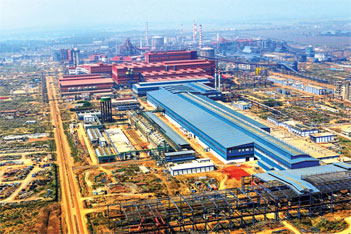
Tata Steel Kalinganagar
STRATEGIC FOCUS AREA
Growth to meet customer requirements and create value
STAKEHOLDERS
Customers
Investors
OUR GOAL
Ramp-up capacity
Preferred choice of supplier in the
chosen segment
ENABLERS
Ramp-up and stabilise new facilities
Value-added products, services & solutions
Reduce defects to < 100 ppm
CAPITALS IMPACTED

UN SDG
8 – DECENT WORK & ECONOMIC GROWTH
Our goal is to achieve 20% of the revenues from services and solutions business. In the last three years, we have built a pipeline of solution concepts that will reach consumers progressively in the coming months and years.
Some of the services and solutions launched/scaled-up in FY2017 are:
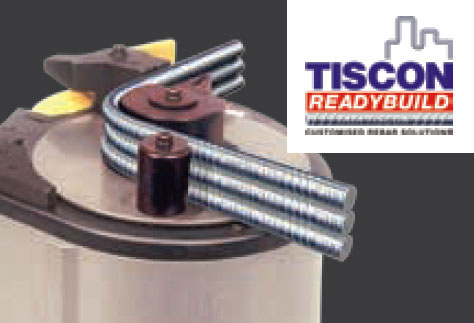
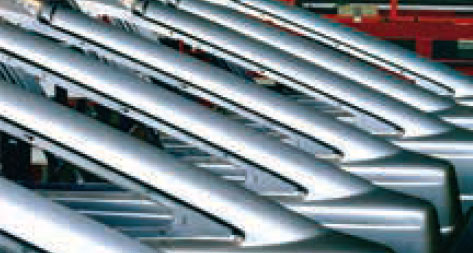
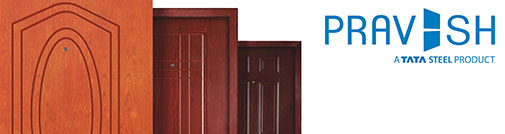
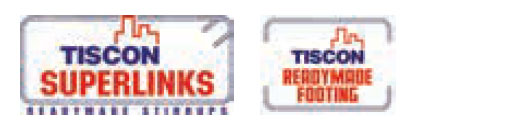
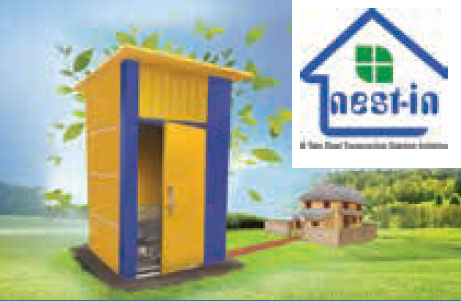
Time Water Kiosks
for upcoming
smart cities and
for corporate CSR
programmes. The
unit is supplied with
a RO+UV filter.
KEY PERFORMANCE INDICATORS

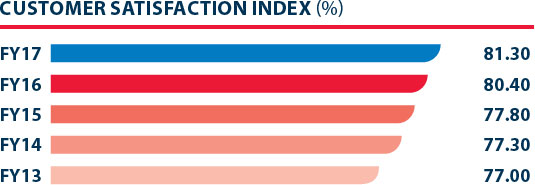
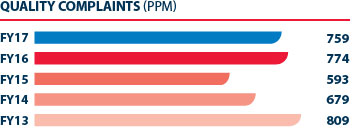
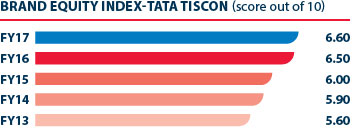
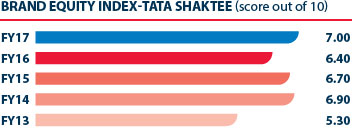
CONTINUOUS DE-COMMODITISATION OF STEEL HAS BEEN THE CORNERSTONE OF TATA STEEL INDIA BRANDING JOURNEY
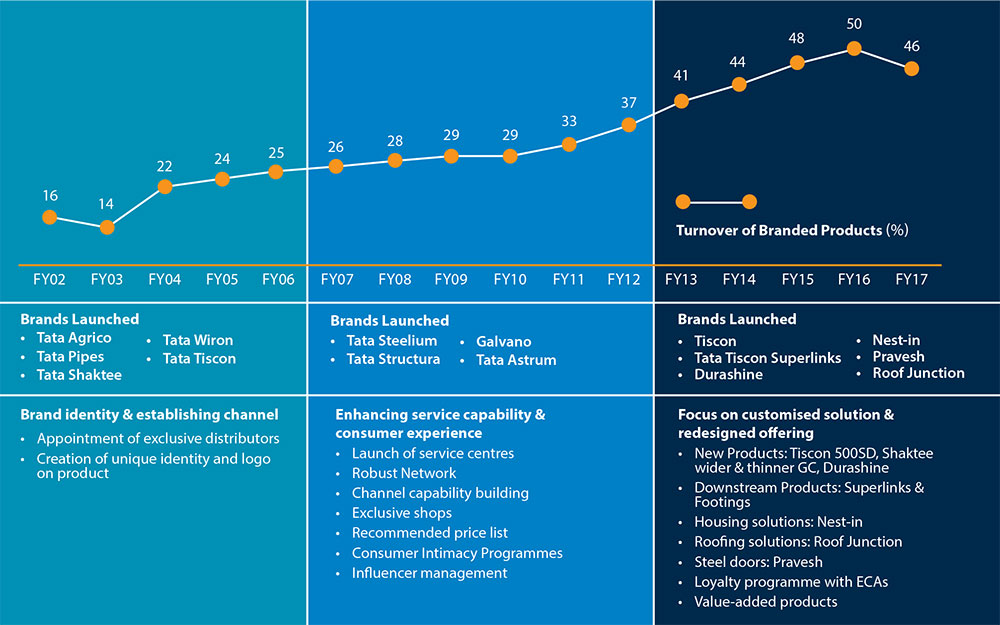
Note: Drop in FY17 as new greenfield project at Kalinganagar is in the ramp-up Phase.
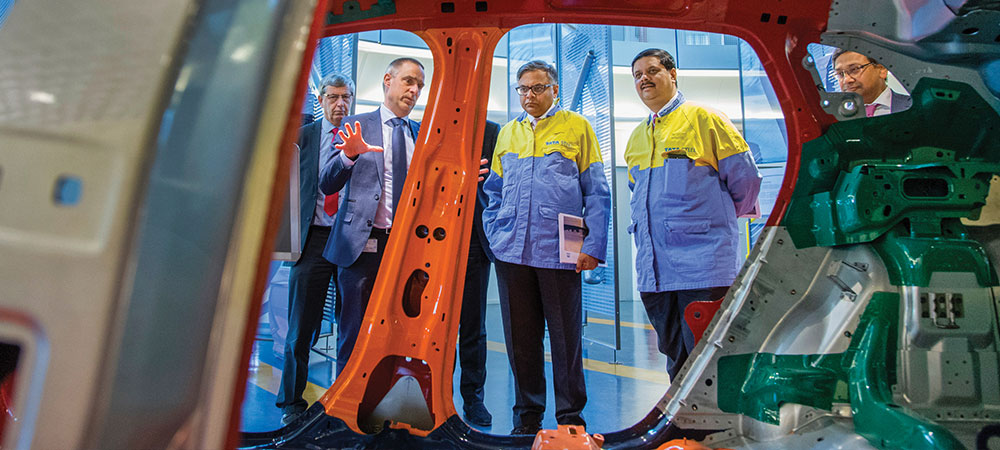
Chairman's visit to IJmuiden facility
Operational Excellence
We aim to retain our position as one of the lowest cost steel producers in the world through improved operational efficiencies and business excellence. We have a long value chain spanning across mining, iron-making, steel making, casting, rolling, finishing and delivering finished steel products to the customer. While this makes it a complex business, it also offers opportunities for improvement across the value chain. Our main focus areas are achieving superior steel properties, higher efficiency in iron ore & coal beneficiation, lower carbon rate in iron making, optimised product mix, reducing waste generation, energy efficient processes and higher material utilisation.
To expedite projects related to operational excellence across the value chain, in FY2015, we launched the Shikhar25 programme. It aims to identify and accelerate improvement projects across the value chain and achieve benchmark levels while building institutional capability. A total savings of `3,400 crore was achieved in FY2017 as a result of all improvement initiatives.
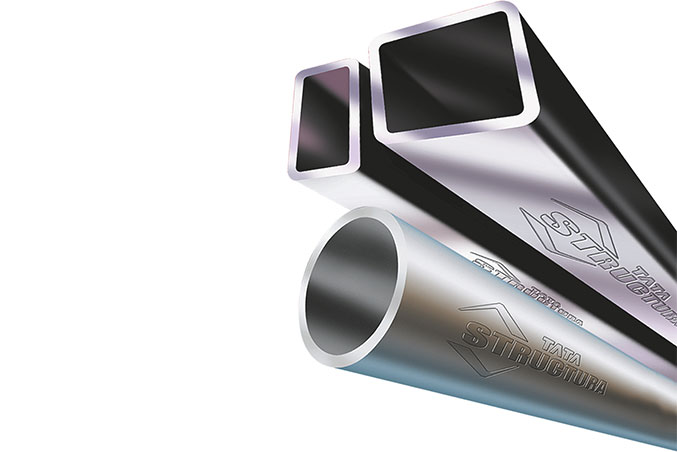
STRATEGIC FOCUS AREA
Cost Leadership and Business Excellence
STAKEHOLDERS
Investors
Suppliers
Customers
OUR GOAL
To become the lowest cost steel producer
ENABLERS
Widen scope and maintain rigor of improvement initiatives through SHIKHAR
Reduce procured raw material and services cost
Enhance captive coal production Double employee productivity Improve efficiency of material use and Increase recycling.
CAPITALS IMPACTED

UN SDG
8 – DECENT WORK & ECONOMIC GROWTH
KEY ACHIEVEMENTS
RAW MATERIALS
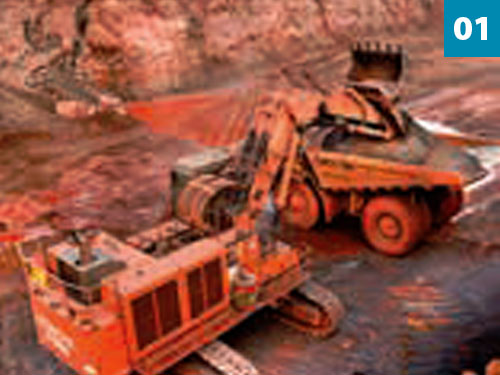
Own captive coal throughput increase was prioritised to replace imported coal.
The key initiatives were:
Coal yield optimisation
Debottlenecking of rail and vessel logistics and raw coal evacuation
Maximisation of West Bokaro washeries utilisation
IRON-MAKING
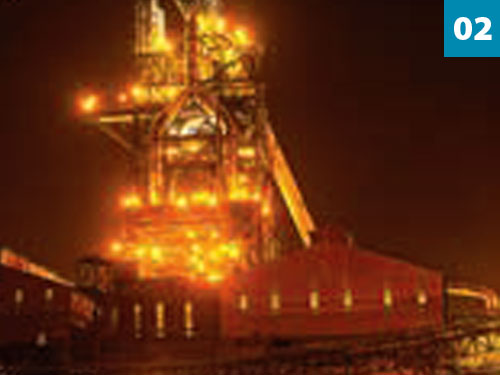
Reduction in Coke rate and hot metal Silicon
Increase in net sinter production through process stabilisation and reliability improvement
Improving performance of Pollution control equipment
STEEL MAKING
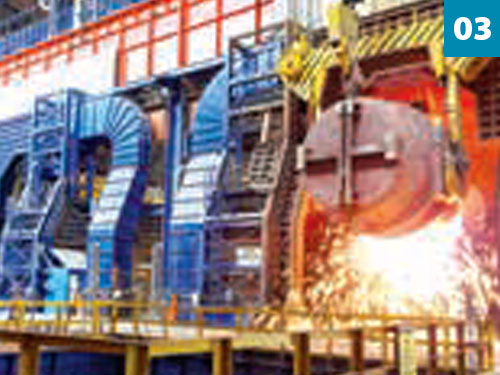
Reduction in transition losses using optimisation models at steel making shop - LD2.
The model identifies best possible grade/chemistry to be produced, checks the order availability, and guides the steel maker to modify the plan accordingly
LOGISTICS
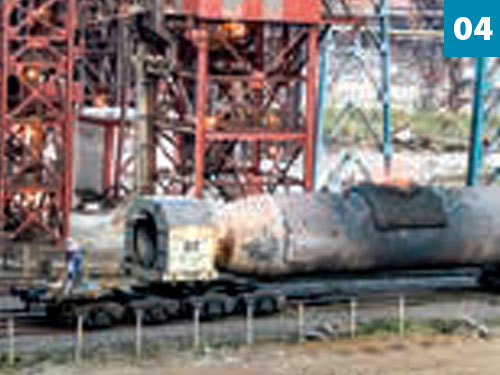
Reduction in landed logistics cost by 12% compared to the previous year
Restructuring of legacy contracts with key suppliers at ports
Reduction of idle freight across mines, collieries, ports and HMC by Installation of IR certified in - motion weigh bridge, Load cells in payloaders, increased height of loading in coke wagons
Consolidation of cargo with third parties and trans-shipment
KEY PERFORMANCE INDICATORS
OPERATIONAL EXCELLENCE
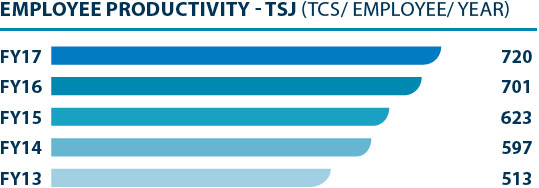
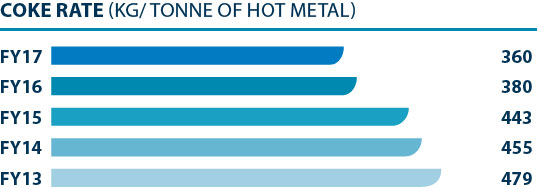
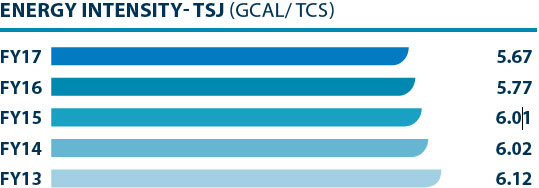
TCS: Tonnes of Crude Steel
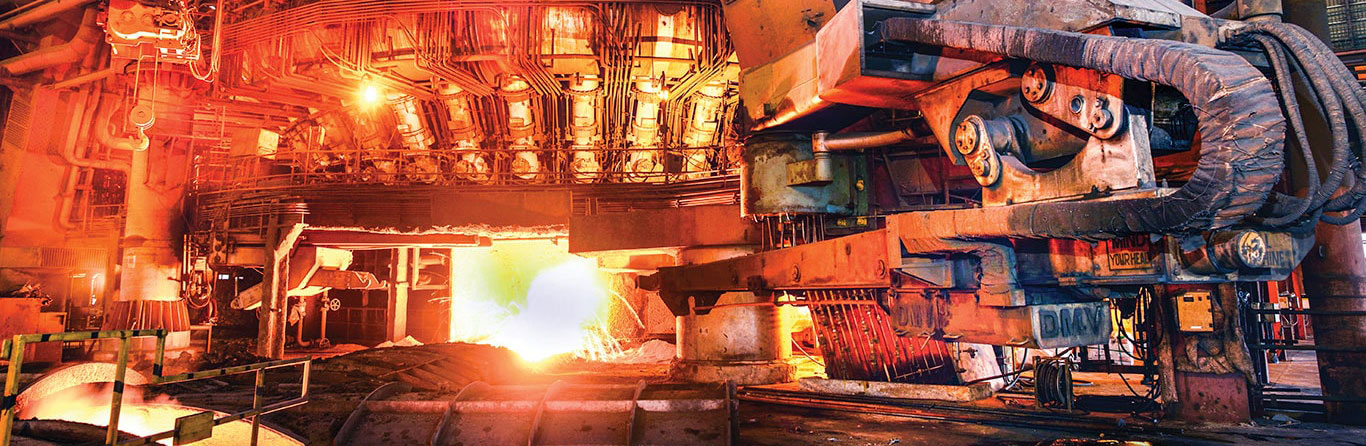
Blast Furnace, Tata Steel Kalinganagar
Apart from leveraging our technological capabilities to address inferior quality of indigenous raw material and the variability of domestic ore compared with imported raw materials, we continuously aspire to be at the high end of technological capabilities and strive to meet high-quality product requirements as and when the evolving demand for newer, high-strength grades of steel arises.
Our focus is on reducing our carbon footprint, optimally use inferior raw materials, improve yield, utilise solid waste and move towards a system of Zero Water Discharge. Our efforts in innovation can be broadly classified into four categories: New Product Development, Process Technology, Digitalisation and Advanced Materials.
01 New Product Development
We are pursuing new products to be developed under the two categories:
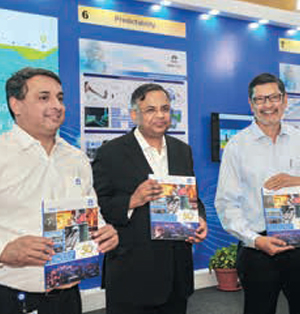
Development of Hot Rolled Dual Phase (DP) Steel, characterised by high-strength and high-formability, is a major step towards meeting the expectations of automotive wheel manufacturers. To address the issues related to automotive wheels with a higher fatigue-life, we developed hot rolled Dual Phase steel with a minimum 600 MPa strength (DP 600) for the first time in India. Apart from high-strength, the grade showed enhanced formability compared with other existing High-Strength Low Alloy steels (HSLA) of similar strength.
Our in-house R&D team achieved this by using advanced thermo-mechanical simulator Gleeble 3800 for hot rolling simulations, by adopting innovative cooling strategies in our Thin Slab Casting and Rolling (TSCR) mill and by making use of longer Run out Table (ROT) with higher cooling capacity. DP steel has cleared stringent requirements of corner fatigue tests that have been conducted at customers’ facilities. Another variant of DP 600 steel was developed with low silicon content to achieve superior surface quality. Both the grades have been accepted by our customers and commercialised by us. Two patent applications have also been filed.
STRATEGIC FOCUS AREA
Technology & Innovation
STAKEHOLDERS
Investors
Customers
Suppliers
OUR GOAL
To be one of the top 5 steel technology companies in the world
ENABLERS
Commercialisation of Graphene and creation of new materials business vertical
Reduce procured raw material and services cost
Technological initiatives in the areas of process efficiency and product development
Creating value through digitalisation
CAPITALS IMPACTED
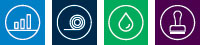
UN SDG
9-INDUSTRY, INNOVATION &
INFRASTRUCTURE
02 Process Technology
One of the key enablers of sustainable mining and lower-cost of liquid iron has been the utilisation of high gangue iron ore in our sinter making process. The high gangue material (with iron content of ~55%) requires significant area for stacking as well as the addition of flux (pyroxinite) for the removal of gangue from metal during the sintering process. Earlier, the flux used to be imported, driving up costs considerably. A new process was developed to use high siliceous gangue material in the sinter using a locally sourced material as flux. Consumption of imported flux decreased by 5.5 kg/tonne with no adverse impact on sinter quality. This led to savings of `12.5 crore per annum.
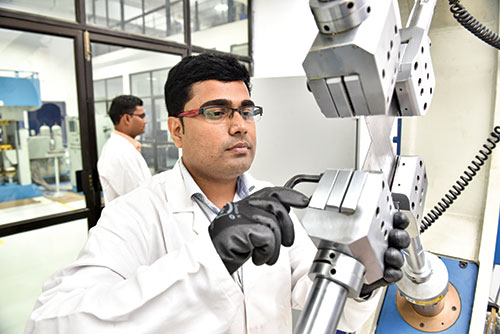
Some of the other examples of process improvement are:
For utilisation of low-grade chromite ores for sustaining standard concentrate production, a new method of operational philosophy established in the chromite ore beneficiation plant at Sukinda.
Increase in clean coal production from reflux classifier by changing the feed regime and rectifying machinerelated issues at West Bokaro Washery #3.
Utilisation of BF slag as flux in chromite pelletising along with improvement in pellet property.
Reduction in water consumption (0.2 m3/tcs) in Jamshedpur Steel Works through multiple recycling of water in high temperature processes.
5% use of non-coking coal in Haldia Met Coke to minimise blend cost and reduce import of coal.
03 Digitalisation: Leveraging Digital Technology
We appreciate the disruptive potential of Industry 4.0 and are actively seeking opportunities to redefine existing processes and systems by leveraging digital technologies. The year saw a significant upgrade in the discourse around digitalisation along with a rich project pipeline created for delivering business value in the coming years.
During FY2017, we identified opportunities for value creation worth `700 crore using digital technologies. The projects include Predictive Asset and Quality Management at process plants, Digitalisation of Customer Decision Journey in the Retail Segment as well as developing Smart-City Applications.
Jamshedpur has also become the first city in India to have a 3-wall-depth penetration of Low Power Wide Area Network (LPWAN), forming the foundation for development of Smart City Applications. Applications under development include - smart metering for power and water, intelligent street-lighting and smart waste bin management.
We have adopted advanced analytics as a key tool to take operating efficiencies to the next level. Advanced Analytic-based predictive models are now powering critical plant functions, examples of which are:
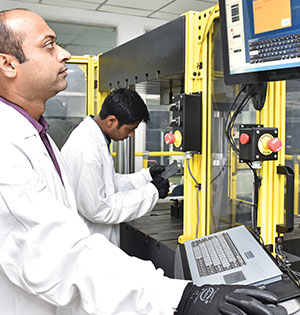
Steel making
Enhancement Break-out Detection System
at LD Slab Caster to improve throughput
and eliminate unsafe conditions through
advanced data analytics.
Tubes Business Unit
A Predictive Asset Maintenance solution
enabling higher equipment availability
and a Salesforce application for dealers to
improve effectiveness and efficiency.
New Bar Mill
Integration of QR Codes onto critical
equipment enabling equipment data
availability on a smartphone. Designated
employees can monitor equipment health
right on the shop-floor and perform
on-site diagnostics.
Having established a dedicated team to drive the transformation to becoming an Industry 4.0 leader, we also facilitate the development of organisational capabilities around digital technologies and data analytics. We are in the midst of upgrading to SAP S4 HANA platform that will simplify and improve business processes.
04 Advanced Materials
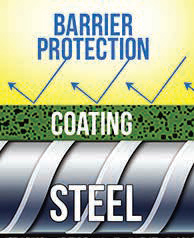
Graphene
Graphene - a material offering substantial superior anti-corrosive properties, enhanced product aesthetics and a wide range of applications - has been identified as one of the advanced materials that has the potential to multiply value across segments. The Indian Graphene market (`80 crore) is currently in a nascent state with immense potential. The steep rise in graphene application patents further supports the realisation of an industrial market in the upcoming years.
A Graphene Development Cell (GDC) has been created at Jamshedpur to identify applications and establish new business (production units, supply chain and markets). Two Advanced Materials Research centres of excellence have been established at Chennai in collaboration with IIT Madras and at Bengaluru with CeNS for collaboration on basic research on Graphene and other 2D materials.
GDC has developed and implemented Graphene powder and Graphene-based liquid that acts as the input to Graphene based products. Graphene coated stirrups were launched under the brand name SUPERLINK+ in Jharkhand. SUPERLINK+ has enhanced corrosion resistance and better bonding strength with concrete as compared with existing stirrups in the market. Seven patent applications have already been filed in this area of work.
KEY PERFORMANCE INDICATORS
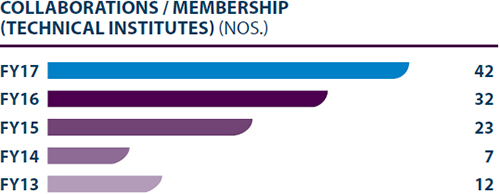
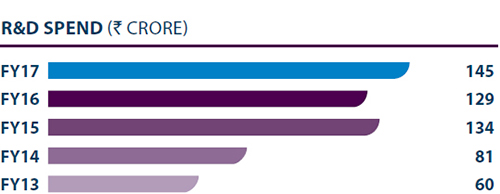
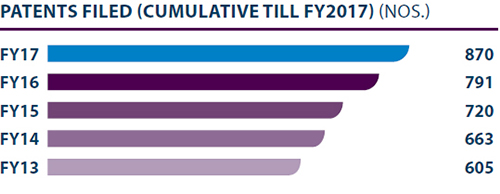
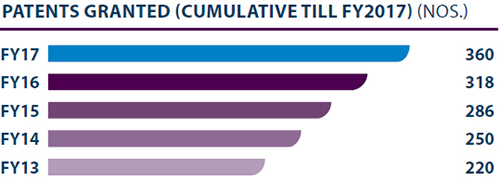
We aspire to be the Indian steel industry benchmark for environment performance by focusing on climate change mitigation and resource efficiency. The key natural resources on which our operations are primarily dependent on are: coal, iron ore, water and ferro alloys.
We are cognisant of the fact that our mining operations impact the biodiversity of the regions in which we operate. Environmental impacts of our manufacturing operations include generation of CO2, dust emissions, discharge of water effluents and process waste generation.
To address these impacts, our policies for climate change mitigation, environmental care, energy efficiency and renewable energy provide overall guidance to our processes and help us achieve environmental leadership.
Environment management of key sites involved in mining and manufacturing are certified under EMS ISO 14001. The Company continues to be a Climate Action Member of the World Steel Association and endorses the United Nations Global Compact's SDGs and CEO Water Mandate.
Some of the thrust areas for environmental excellence are:

Concerted R&D efforts to conserve natural resources

Climate change impact mitigation

Reduction of our resource footprint through ore beneficiation

Material substitution

Continual process improvement and product development

Revision of the Energy Policy to explicitly embed the promotion of renewable and non-conventional energy
SHADOW CARBON PRICE
We believe any capital investment should be made after evaluation of its climate impact. To enable this, we have introduced the Shadow Carbon Price, which will be used for evaluating any capital expenditure projects in Tata Steel
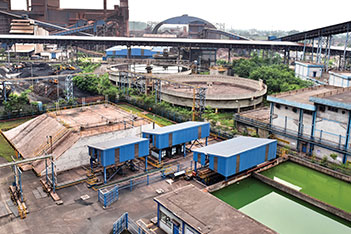
Central Effluent Treatment Plant
STRATEGIC FOCUS AREA
Environment Leadership
STAKEHOLDERS
Government
Regulatory Bodies
Customers
Civil Society
OUR GOAL
Become industry benchmark in environmental performance
ENABLERS
Reduce CO2 emission intensity
< 2tCO2/tcs
(tcs: tonne of crude steel)
Zero effluent discharge
100% utilisation of LD Slag
Increase use of renewable energy
No net loss of targeted Biodiversity components in raw material locations and progressive reclamation of mine altered sites
CAPITALS IMPACTED
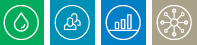
UN SDG
7 - AFFORDABLE
& CLEAN ENERGY
UN SDG
13 - CLIMATE
ACTION
UN SDG
12 - RESPONSIBLE PRODUCTION &
CONSUMPTION
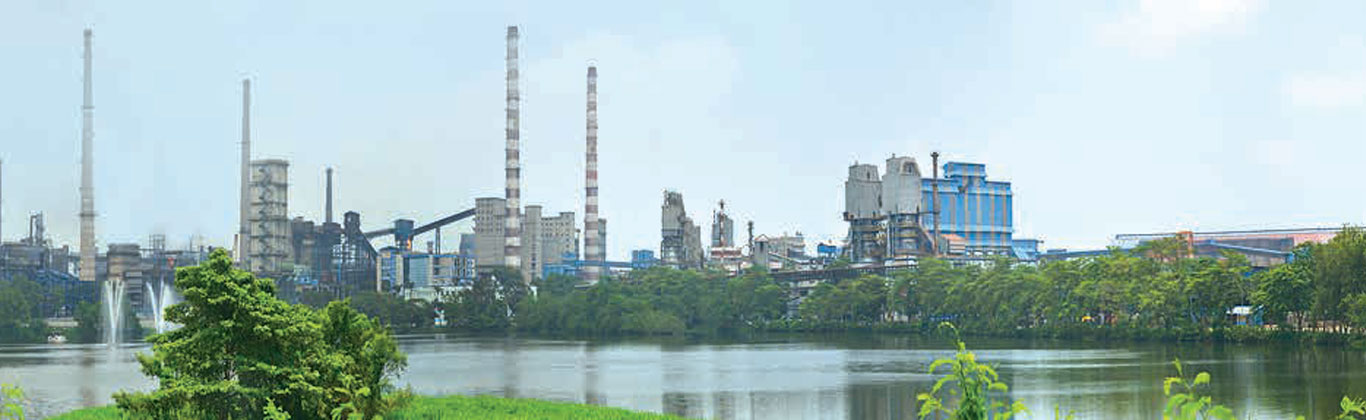
Tata Steel Jamshedpur
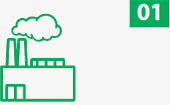
CO2 EMISSION
Energy conservation through: Top Recovery Turbine (TRT) power generation
LD Gas recovery
Reduction in carbon rate
LD Gas recovery enhanced by 44%
of Carbon rate
within Steel Sector (Coal based Integrated Works, BF-BOF)
in CO2 emissions in FY2017 (base level in FY2005
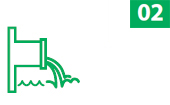
WATER CONSUMPTION AND ZERO EFFLUENT DISCHARGE
Water conservation initiatives at operational facilities
Improved utilisation of Central Effluent Treatment Plant
over previous year at our Jamshedpur Steel Works
~16% reduction
over FY2016
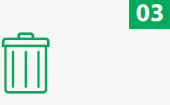
SOLID WASTE UTILISATION
Zero waste mining driven by ore characterisation, ore-body modeling, and block modeling of mining deposits done, Life Cycle Inventory (LCI) studies for mines
State-of-the-art beneficiation plants in operation and studies underway for beneficiating slime and low-grade ores
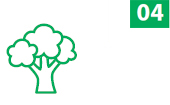
BIODIVERSITY
Rollout of Biodiversity Management Plans (BMPs) for each of the eight mining sites
Assessment of habitats using the Biodiversity Indicator and Reporting System (BIRS) tool undertaken
in targeted biodiversity components from pre‐mine conditions
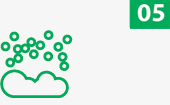
DUST EMISSION
Up-gradation of pollution control equipment
Engagement of OEMs for effective operation & maintenance
KEY PERFORMANCE INDICATORS
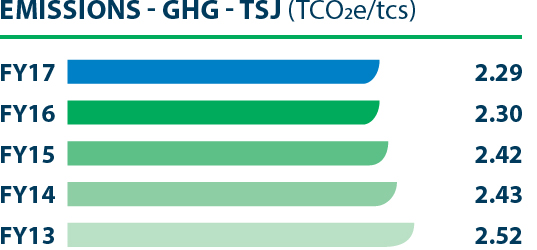
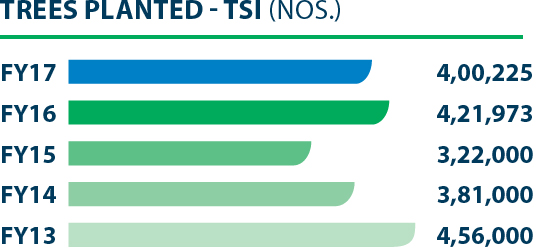
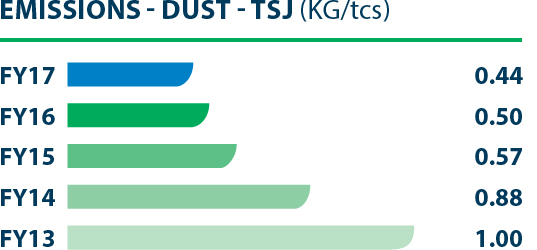
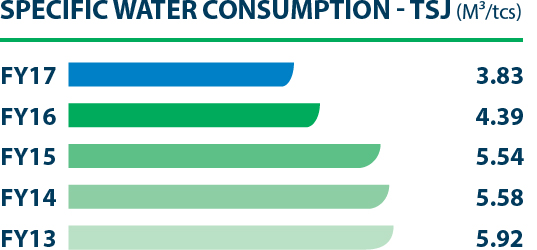
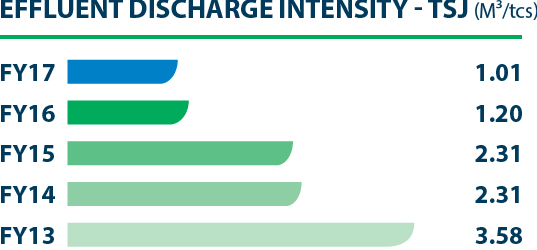
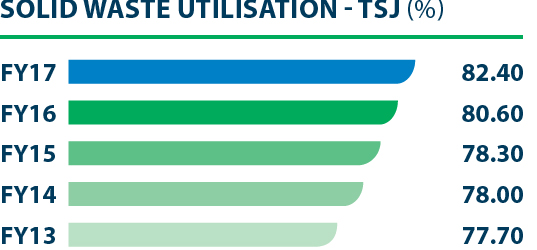
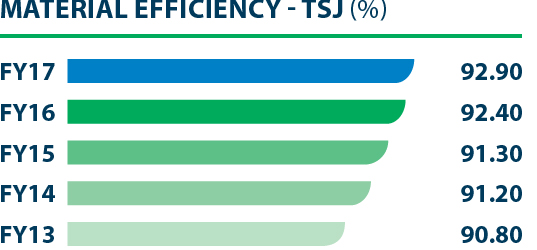
We are aware that the regions that we operate in are largely socio-economically backward and have been impacted by political unrest. An overwhelming majority of the population in these regions is dependent upon rain-fed, single-crop agricultural produce for their livelihood. A major concern in these regions is the development of the Scheduled Castes (SC) and Scheduled Tribes (ST) who constitute a major percentage of the population. We promote Affirmative Action based on positive discrimination to improve levels of education, employment, employability, entrepreneurship, while preserving the ethnicity of this section of the population.
The Tata Steel CSR Advisory Council comprises eminent personalities from academia and development sector, who provide policy-level inputs for improvement of our CSR interventions. The priority areas for improvement identified in Jharkhand and Odisha are health, education and livelihood. The other areas of intervention are skill development, ethnicity, water, civil infrastructure and sports.
Thousand Schools Project
This ambitious project aims at making the Right to Education (RTE) Act a reality in six
blocks of three tribal districts of Odisha – Jajpur, Keonjhar, Sundargarh. The project
envisions better access to school for children while improving the quality of education
that they have access to.
Improved teaching quality is imperative for quality education. Some of the key
initiatives in this direction are:
01
Instituting effective classroom pedagogy to strengthen the foundation level learning of children
02
Enhancing teachers' capabilities
03
Making available quality teaching and learning materials in classrooms
04
Setting up of school libraries and introducing tabletbased classroom content
05
Establishing an effective academic monitoring mechanism
06
Enabling proper functioning of School Management Committees (SMCs), mandated by the RTE Act to have oversight of school functioning and performance
We have carried out numerous activities like staff orientation, training for teachers and the youth. We also trained the School Management Committees (SMCs) and members of Panchayati Raj Institution. We are implementing the project in partnership with Delhibased NGO ASPIRE.
1. 22,000 children have been positively impacted through this project
2. 400 habitations are child labour free across the six project blocks
3. 6,375 out of school children have been mainstreamed into education
4. 3,646 children have been helped to transition from primary to middle school
5. 12,705 school going children of primary classes have been helped to improve
their learning levels significantly in Language and Maths (evidence-based)
STRATEGIC FOCUS AREA
Impact Based CSR
STAKEHOLDERS
Government
Regulatory Bodies
Community
OUR GOAL
Positively impacting
>2 million lives
ENABLERS
Expand reach and impact of our Initiatives in areas of Health, Education, Livelihood, Water and Civil Infrastructure, Skill Development, Sports and Ethnicity
Leverage collaborative and financing opportunities
CAPITALS IMPACTED
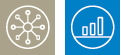
UN SDG
11- SUSTAINABLE CITIES &
COMMUNITIES

Thousand Schools Project, Odisha
KEY INITIATIVES
EDUCATION Improving the access and quality of education for all and scholarships for meritorious students
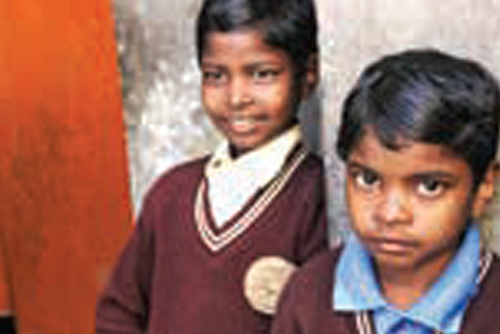
30 MODEL SCHOOLS
Construction of 30 model schools in 30 blocks in Odisha
Spend of over
`29 Cr.
to the State Government in FY2017 with the required classroom infrastructure
Another five are ready for handover
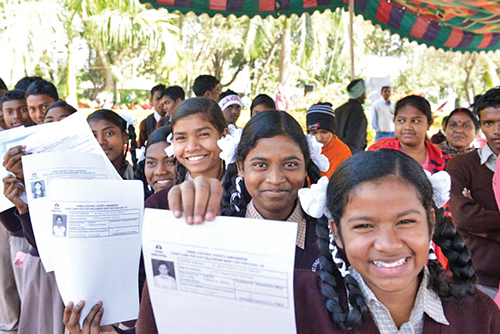
JYOTI FELLOWSHIP
Scholarships to meritorious SC/ST students
in FY2017 over 2,883 in FY2016
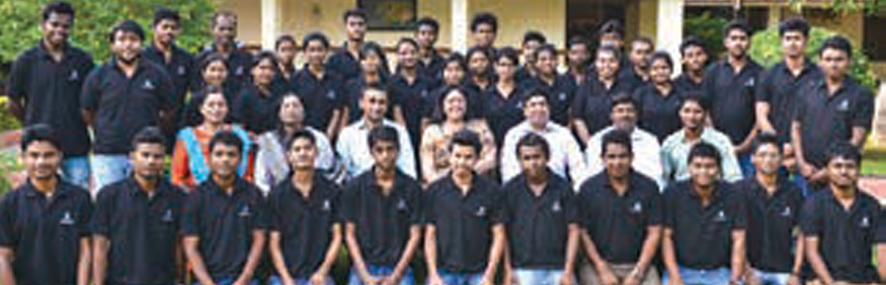
TATA STEEL SCHOLARS PROGRAMME
Assistance for professional education to meritorious SC / ST students
in FY2017 over 83 in FY2016
SPORTS & ETHNICITY Preserving culture
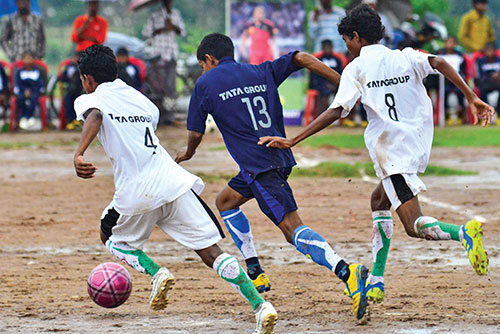
UNDER 10 FOOTBALL TRAINING CENTRES
Training at Tata Steel-backed football training centre
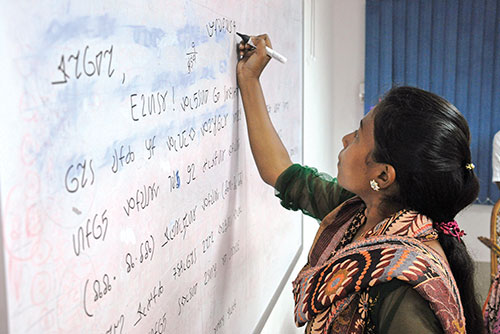
TRIBAL LANGUAGE LEARNING CENTRES
Promotion of tribal languages and literature
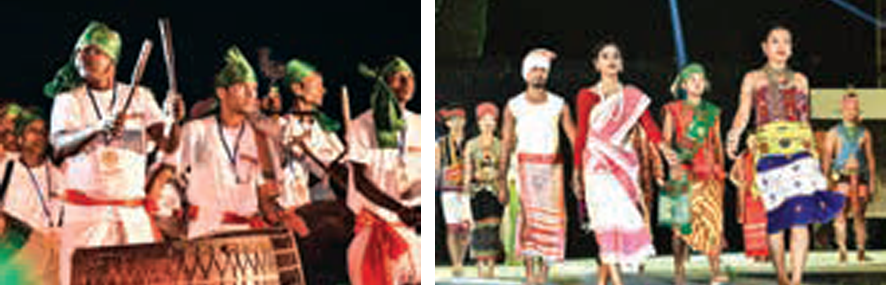
PRESERVE AND PROMOTE TRIBAL
CULTURE AND
HERITAGE
Tribal Conclave
HEALTH Primary healthcare, maternal and child healthcare, specialised healthcare and adolescent health programmes
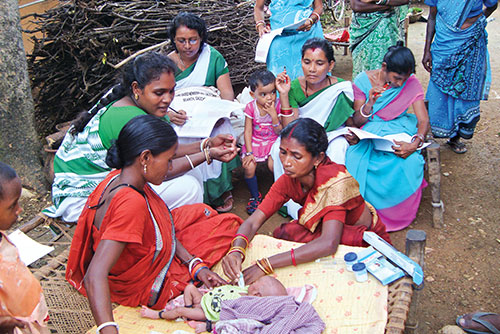
MANSI
Maternal & Newborn Survival
Initiatives
A PPP model based initiative to train Government appointed village level women heath workers and increase their capabilities to work towards reducing neonatal and infant mortality
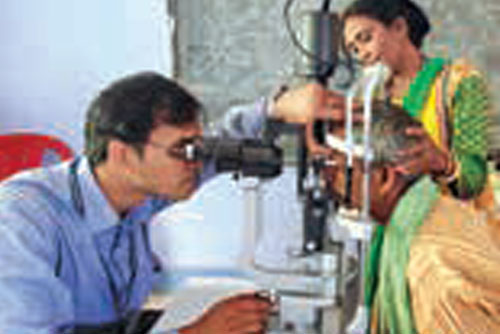
MESU
Mobile Eye Surgical Unit
A collaborative venture between Sankara Nethralaya and IIT Madras, supported by Tata Trusts and Tata Steel provides state-of-the-art cataract surgery in remote areas

MMU
Mobile Medical Units
Tata Steel mobile clinics, deployed in areas deprived of a proper clinic/dispensary, to provide basic consultation and medicine
benefitted through mobile medical units in FY2017 (5,33,597 in FY2016)
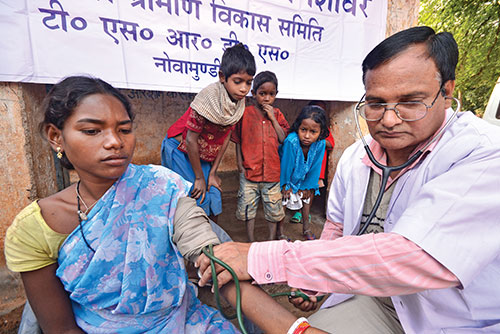
SPECIALISED HEALTH CAMPS FOR FOCUSED ILLNESSES
Specialised camps are held periodically in remote locations to address specific diseases prevalent in these areas
in FY 2017 (129 camps and 30,537 beneficiaries in FY2016)
SUSTAINABLE LIVELIHOODS Enabling people
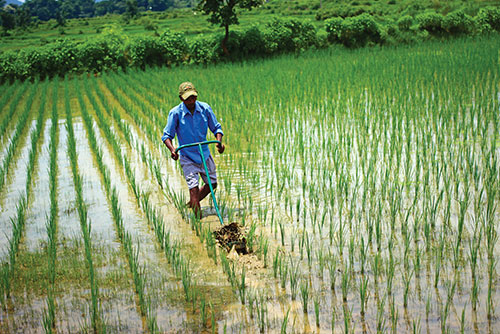
SYSTEM OF RICE INTENSIFICATION (SRI) METHOD OF PADDY CULTIVATION
Working with farmers to deploy scientific agriculture techniques leading to improvement in paddy yield
trained in FY2017 on the SRI method (8,350 in FY2016)
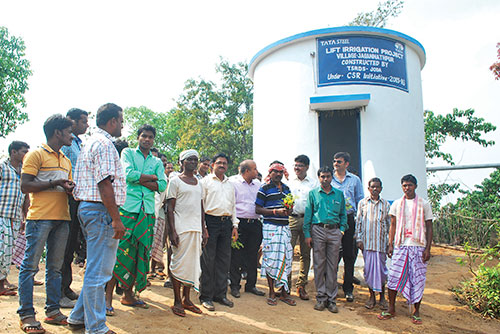
FARMERS’ TRAINING IN VEGETABLE CULTIVATION
Improving cropping efficiency and maximising use of irrigation facilities
trained in FY2017 (4,238 in FY2016)
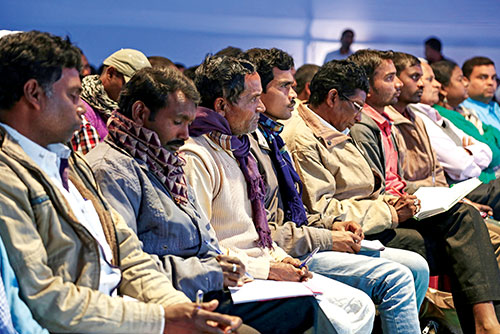
VAARTA
Agricultural Meet
Supporting farmers in undertaking modern agriculture by regular interface with agricultural scientists
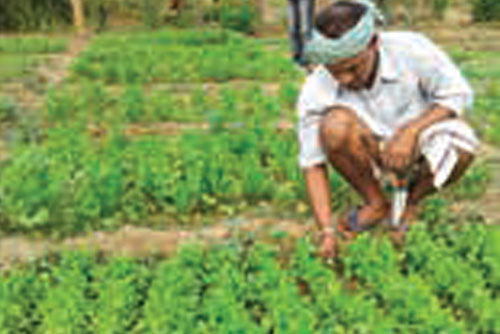
LIVELIHOOD INTERVENTIONS THROUGH COLLECTIVES FOR INTEGRATED LIVELIHOOD INITIATIVES (CInI)
Livelihood interventions in agriculture and knowledge transfer through CInI
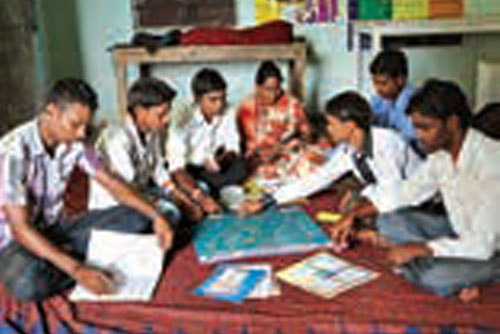
RISHTA Regional Initiative For Safe Sexual Health For Today’s Adolescents
Adolescents counseled on sexual health through school sessions and Youth Resource Centres
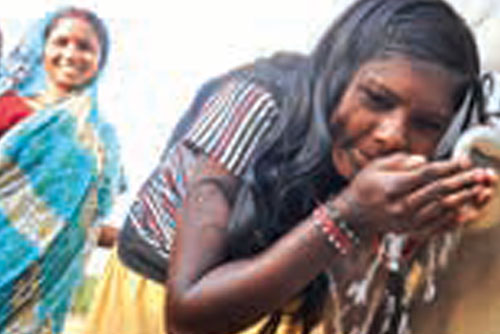
BOKARO RIVER DRINKING WATER PROJECT
Rainwater harvesting based project with a dam along with an intake well, capable of supplying approximately 1,000 kilo litres of filtered and chlorinated water per day
since the inception of MANSI in FY2010
since the inception of MANSI in FY2010
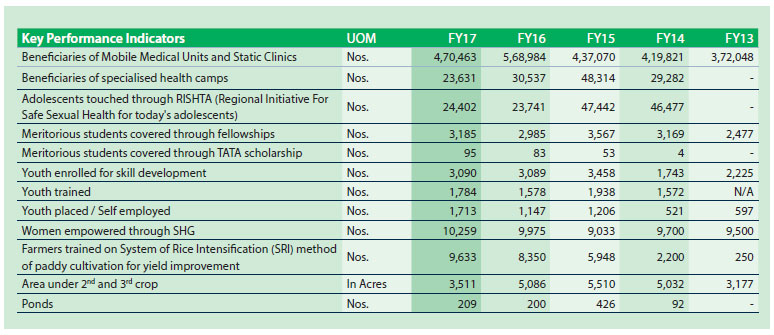
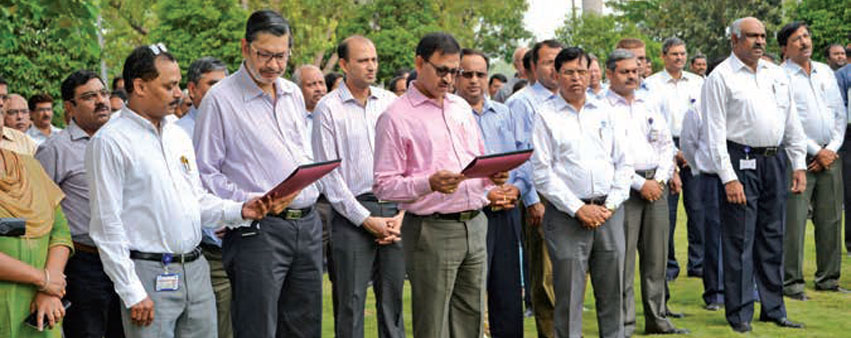
Ethical behaviour is intrinsic to the way we conduct our business. The Tata Group’s founder, Jamsetji Tata, insisted that business must respect the rights of all its stakeholders and create an overall benefit for the society.
Our corporate values of unity, responsibility, excellence, pioneering and integrity are the guiding principles by which we strive to conduct our business.
Our governance framework flows from our Code of conduct and policies. The framework is designed to ensure that our business is conducted in an honest and ethical manner, with integrity and it conforms with the relevant laws and regulations of the countries where we operate in.
Tata Code of Conduct
All Tata Group companies subscribe to the Tata Code of Conduct (‘Code’), which clearly articulates our ethical principles and desired behaviours. The Code requires the Tata companies and employees to act with professionalism, honesty and integrity and to preserve the human rights of every individual and the community. The principles of the Code apply to all our dealings with our business partners who are encouraged to adhere to similar standards. The Code covers various subjects like equal opportunity employer, dignity & respect, human rights, bribery & corruption, gifts and hospitality, conflict of interest, financial reporting and records among others.
The Tata Code of Conduct is augmented by a number of policies that help strengthen governance practices at Tata Steel. These policies include the Conflict of Interest Policy, The Policy for Receipt of Gifts and Hospitality, The Whistle Blower Policy and the Prevention of Sexual Harassment at Workplace Policy.
Affirmative Action
In accordance with its Affirmative Action Policy, Tata Steel encourages business entrepreneurs from socially disadvantaged communities and includes them in its supply chain on the basis of equal merit. The Company has leveraged its growth projects to diversify its workforce through positive discrimination in favour of local, marginalised communities and women. Also, Tata Steel chooses organisations aligned to its Affirmative Action Policy as its Strategic Sourcing partners.
Building Blocks of Responsible Procurement
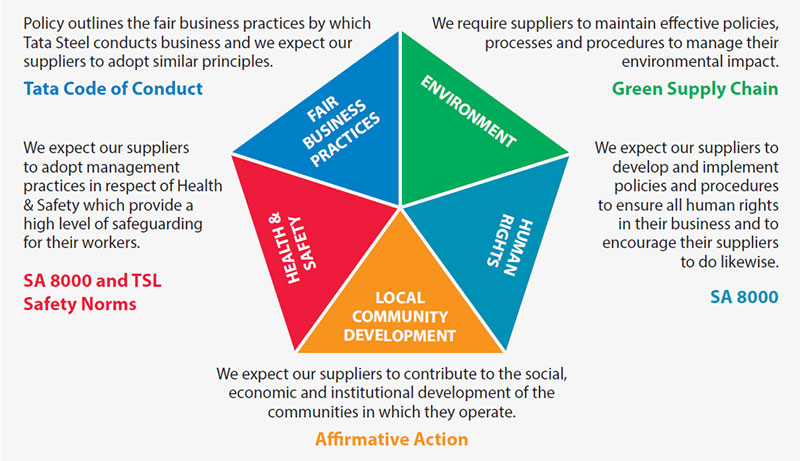
3,281 Officers
14,430 Non-Officers
22,069 Contractors' Employees'
1,085 Vocational Trainees
1 POSH- Prevention of Sexual Harassment
2 COI- Conflict of Interest
3 TCOC- Tata Code of Conduct
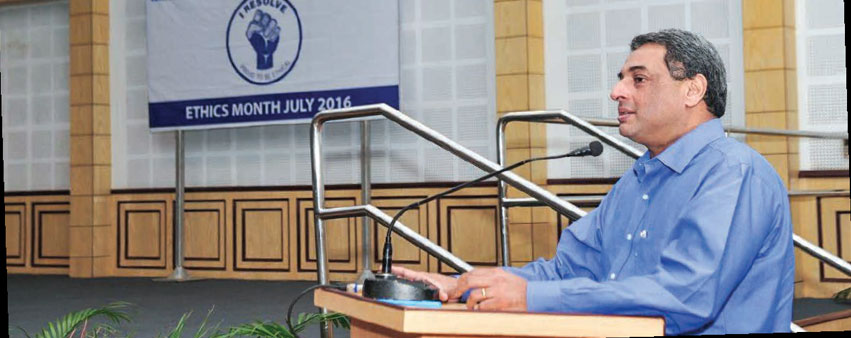
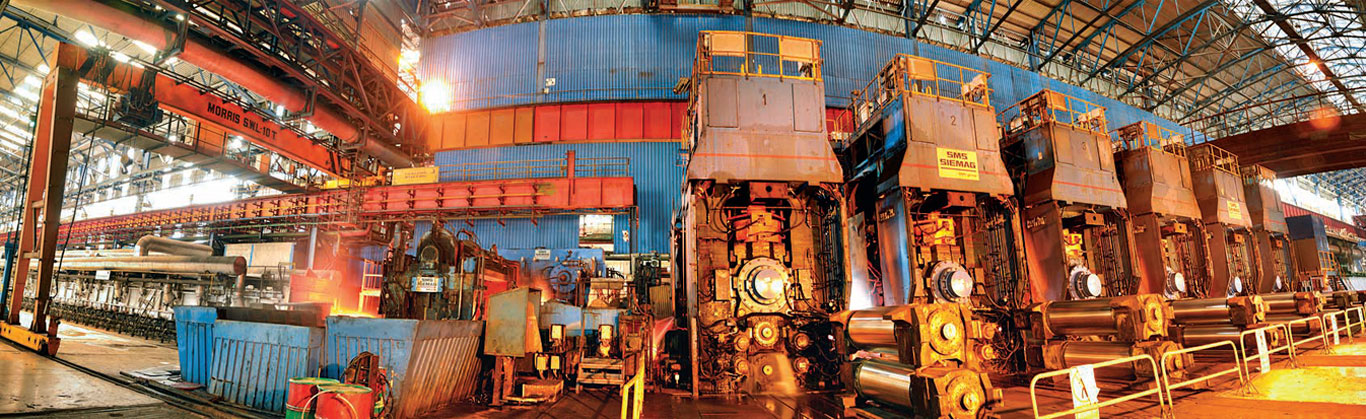
We will continue to seamlessly deploy our strategy, heading towards the goals set for each of our strategic focus areas.

Safety - Zero injury and fatality
We will continue with our efforts of building leadership’s competency, improving contract worker safety management and all other process improvements for identifying safety hazards and mitigating risks, to ultimately reach our goal of Zero LTI

Diversity and Inclusion
With an ambition of having at least 20% women in workforce, we will continue to uphold our ethos of being an equal opportunity employer

Scale-up Services and Solutions
We will aim to ramp-up and stabilise our new operations and continue our efforts towards developing value-added services and products for meeting varied customer requirements

Technology Leadership
We will continue to be the front runners in adoption of new technologies, both in terms of product development and process efficiencies

Climate change strategy: Reduction in specific water consumption and CO2 emission
We will continue to evolve our operational practices and adopt state-of-the-art technologies to increase resource efficiency and reduce emissions

Digitalisation - Realise value and improve stakeholder experience
We will exploit digital technology to the fullest for value enhancement and improving customers’ and partners’ experience. In view of Industry 4.0, we will strive to be ahead of the curve in adopting disruptive digital technologies

Improvement in employee engagement
We will constantly strive to be one of the top quartile ranking companies in the space of employee engagement. We will keep focussing on employee well-being and happiness.

Cost Leadership
With our multi-pronged approach of improving process efficiencies, optimising raw-material usage, waste recycling and employee productivity enhancement, we will keep honing our efforts of cost-leadership